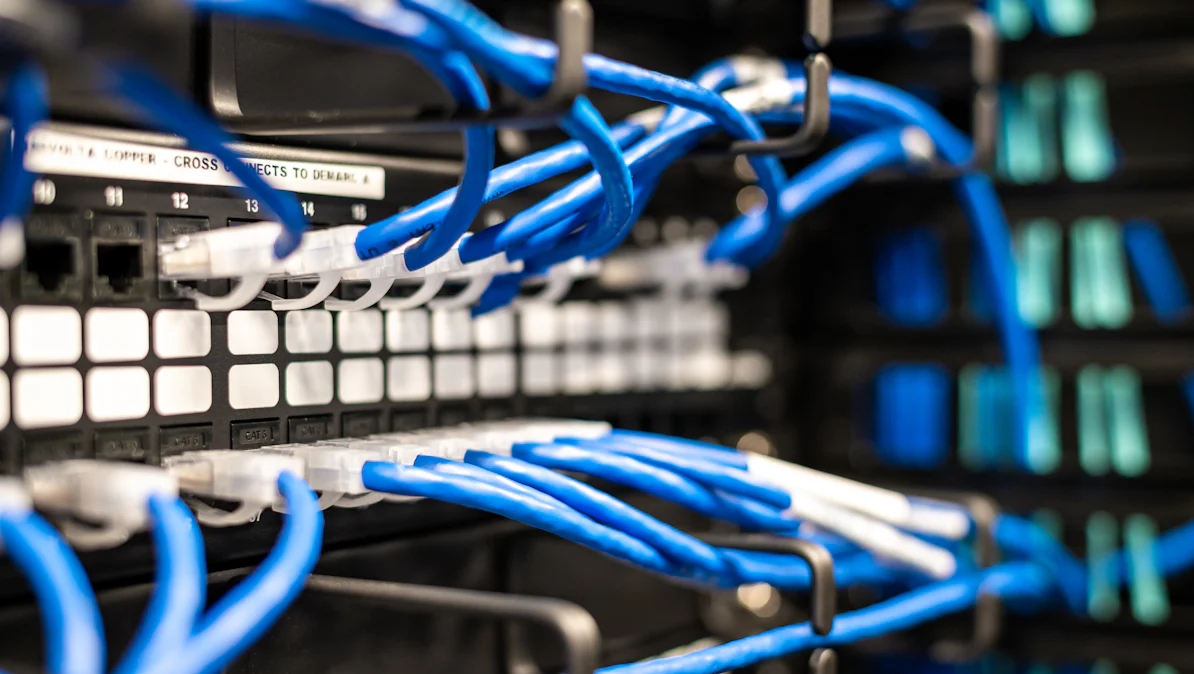
Fiber Optic Cable termination is a crucial process in setting up fiber optic networks. You can achieve this through two primary methods: connector termination and splicing. Connector termination involves attaching connectors to the ends of the Fiber Cables, allowing for easy connection and disconnection. On the other hand, splicing joins two Fiber Cables permanently, ensuring a seamless connection. Each method requires specific tools and techniques, making it essential to understand their applications and benefits. By mastering these methods, you ensure efficient and reliable Fiber Optic Cable connections.
Key Takeaways
- Understand the two primary methods of fiber optic cable termination: connector termination for flexibility and splicing for permanent connections.
- Equip yourself with essential tools like cleavers, strippers, and crimping tools for successful connector termination.
- Choose the right connector type (SC, LC, ST) based on your application needs to ensure reliable connections.
- Follow a step-by-step process for connector termination to achieve optimal performance and minimize signal loss.
- Consider the advantages of both field and factory termination to determine the best approach for your installation requirements.
- Test your connections after termination using tools like visual fault locators to ensure integrity and performance.
- Explore pre-terminated cables from trusted brands like Dowell for reliable, efficient, and high-quality solutions.
Connector Termination for Fiber Optic Cable
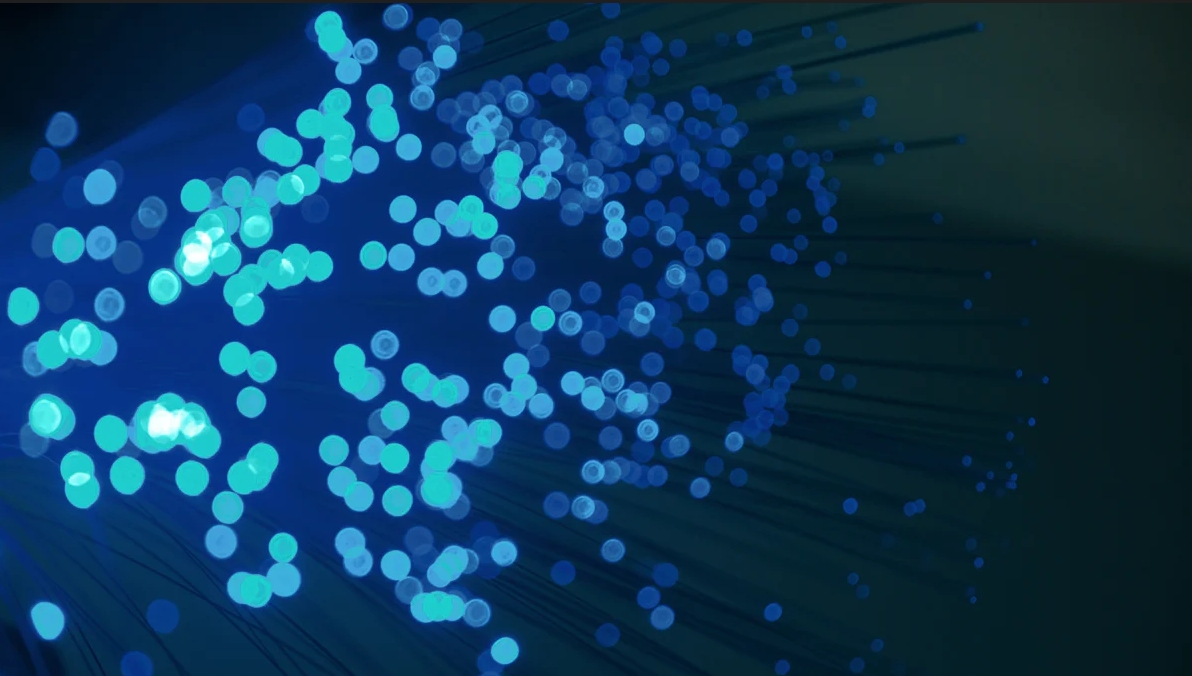
Connector termination is a vital process in the installation of fiber optic networks. This method involves attaching connectors to the ends of fiber cables, allowing for easy connection and disconnection. Understanding the tools and types of connectors used in this process is essential for achieving efficient and reliable connections.
Tools Needed for Connector Termination
To successfully terminate a fiber cable using connectors, you need specific tools:
- Cleaver: This tool is crucial for cutting the fiber cable with precision. A clean cut ensures optimal performance and minimal signal loss.
- Stripper: You use a stripper to remove the protective coating from the fiber, exposing the core for termination.
- Crimping Tool: This tool helps secure the connector onto the fiber, ensuring a stable and durable connection.
Types of Connectors for Fiber Cable
Various connectors are available for fiber optic cable termination, each with unique features:
- SC Connectors: Known for their push-pull design, SC connectors provide a secure and reliable connection. They are commonly used in data communication networks.
- LC Connectors: These connectors are smaller and more compact, making them ideal for high-density applications. Their latch mechanism ensures a stable connection.
- ST Connectors: Featuring a bayonet-style twist-lock mechanism, ST connectors are often used in industrial settings due to their robust design.
Step-by-Step Guide for Connector Termination
Follow this step-by-step termination process to ensure a successful fiber cable connection:
1. Preparing the Cable: Begin by stripping the outer jacket of the fiber cable using a stripper. Carefully expose the core without damaging it. Use a cleaver to cut the fiber to the desired length, ensuring a clean and precise cut.
2. Attaching the Connector: Select the appropriate connector type for your application. Insert the prepared fiber into the connector, ensuring proper alignment. Use a crimping tool to secure the connector onto the fiber, providing a stable and durable connection.
3. Testing the Connection: After attaching the connector, test the connection to ensure optimal performance. Use a visual fault locator or an optical power meter to verify the integrity of the connection. This step ensures that the termination method has been executed correctly and that the fiber optic cable is ready for use.
By following these steps and using the right tools, you can achieve a reliable and efficient fiber cable termination. This process is crucial for maintaining the performance and longevity of your fiber optic network.
Splicing in Fiber Optic Cable Termination
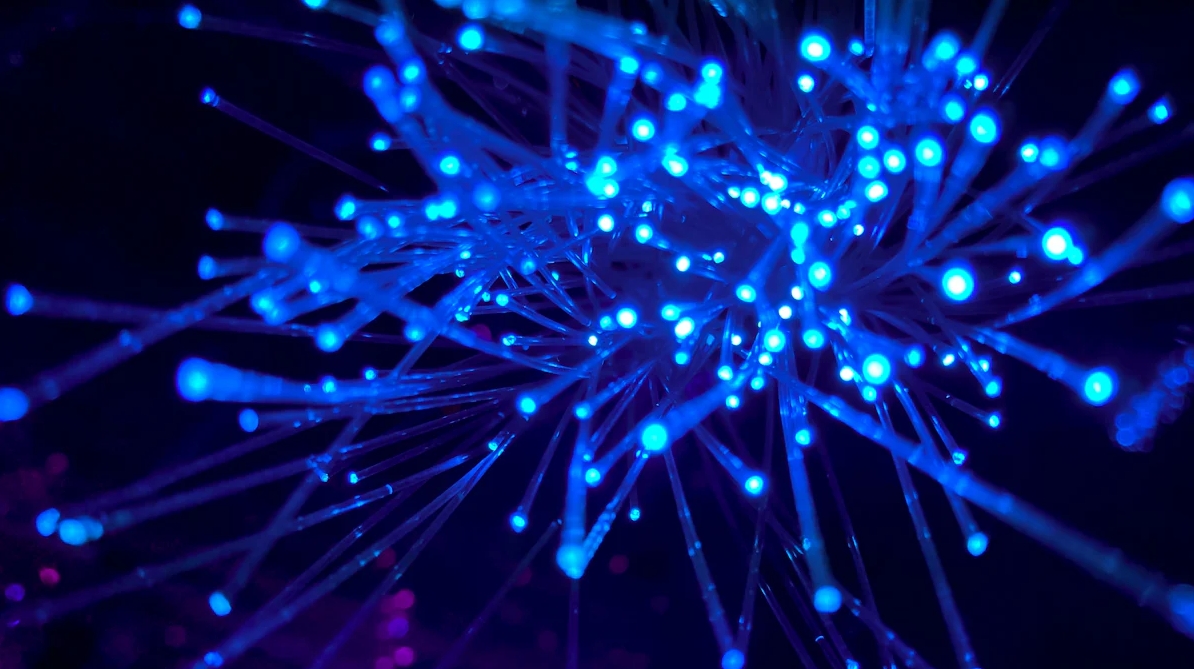
Splicing is a critical termination method for joining fiber optic cables. It ensures a permanent and seamless connection between two fibers. You can choose between two main types of splicing: fusion splicing and mechanical splicing. Each method requires specific tools and techniques to achieve optimal results.
Tools Needed for Splicing
To perform splicing effectively, you need the right tools:
- Fusion Splicer: This device uses an electric arc to weld fibers together, creating a strong and reliable joint.
- Mechanical Splicer: It aligns fibers using a mechanical device, providing a quick and efficient connection.
- Cleaver: Essential for making precise cuts on the fiber, ensuring minimal signal loss.
Fusion Splicing
Fusion splicing is a popular choice for creating high-quality connections. It involves three main steps:
1. Preparing the Fibers: Start by stripping the protective coating from the fiber cable. Use a cleaver to cut the fiber ends cleanly. Proper preparation is crucial for a successful fusion splice.
2. Aligning the Fibers: Place the prepared fibers into the fusion splicer. The device will automatically align the fibers with precision, ensuring a perfect match.
3. Fusing the Fibers: Activate the fusion splicer to create an electric arc. This arc welds the fibers together, forming a strong and durable connection. The result is a seamless fusion splice that minimizes signal loss.
Mechanical Splicing
Mechanical splicing offers a quick and convenient alternative to fusion splicing. Follow these steps for effective mechanical splicing:
1. Preparing the Fibers: Similar to fusion splicing, begin by stripping the fiber cable and cutting the ends precisely with a cleaver.
2. Aligning the Fibers: Insert the prepared fibers into the mechanical splicer. The device will hold the fibers in place, ensuring proper alignment.
3. Securing the Splice: Use the mechanical splicer to secure the fibers together. This method relies on a mechanical device to maintain alignment, providing a stable connection.
Both fusion splicing and mechanical splicing have their advantages. Fusion splicing offers superior optical performance and durability, making it ideal for long-term installations. Mechanical splicing provides a faster and more flexible solution, suitable for temporary or emergency repairs. By understanding these methods, you can choose the best approach for your fiber optic cable termination needs.
Field Termination vs. Factory Termination in Fiber Optic Cable
When it comes to fiber optic cable termination, you have two primary options: field termination and factory termination. Each method offers unique advantages and disadvantages, making it essential to understand which one suits your needs best.
Field Termination
Field termination involves terminating the fiber cable on-site. This method provides flexibility and customization, allowing you to adjust cable lengths precisely according to your requirements.
Field termination involves terminating the fiber cable on-site. This method provides flexibility and customization, allowing you to adjust cable lengths precisely according to your requirements.
Advantages
- Flexibility: You can tailor the cable lengths to fit specific installations, ensuring a perfect fit every time.
- Customization: Field termination allows for adjustments and modifications on-site, accommodating changes in design or layout.
- Immediate Solutions: You can address unforeseen issues or changes in the field without waiting for new cables.
Disadvantages
- Time-Consuming: Field termination requires more time and effort, as you need to perform the termination process on-site.
- Skill Requirement: This method demands skilled technicians to ensure proper termination, which can increase labor costs.
- Potential for Errors: The on-site environment may lead to errors or inconsistencies in the termination process.
Factory Termination
Factory termination involves pre-terminating the fiber optic cables in a controlled environment before installation. This method offers a reliable and efficient solution for many applications.
Advantages
- Quality Assurance: Factory termination ensures high-quality terminations, as they are performed in a controlled environment with precise equipment.
- Time-Saving: Pre-terminated cables reduce installation time, as they arrive ready for immediate use.
- Cost-Effective: This method minimizes labor costs and reduces the risk of errors during installation.
AdvantagesDisadvantages
- Limited Flexibility: Pre-terminated cables come in fixed lengths, which may not always fit your specific needs.
- Longer Lead Times: Ordering pre-terminated cables may require longer lead times, especially for custom lengths or configurations.
- Less Adaptability: Changes or modifications on-site may require additional cables or connectors.
Pre-Terminated Cables by Dowell
Dowell offers pre-terminated cables that combine the benefits of factory termination with the brand's commitment to quality and innovation.
Benefits
- Reliability: Dowell's pre-terminated cables undergo rigorous testing to ensure optimal performance and durability.
- Efficiency: These cables simplify the installation process, reducing time and labor costs.
- Quality: With Dowell's focus on excellence, you can trust that each cable meets the highest standards.
BenefitsApplications
- Telecommunications: Ideal for network installations where reliability and speed are crucial.
- Data Centers: Perfect for environments requiring high-density connections and minimal downtime.
- Infrastructure Projects: Suitable for large-scale projects needing consistent and dependable connectivity.
By understanding the differences between field and factory termination, you can make informed decisions for your fiber optic cable termination needs. Whether you prioritize flexibility or efficiency, choosing the right termination method is key to achieving a successful installation.
In conclusion, understanding the advantages of connector termination and splicing is essential for effective fiber cable management. Connector termination offers flexibility and quick adjustments, making it ideal for dynamic environments. Splicing, on the other hand, provides a permanent and high-quality connection, suitable for long-term installations. Choosing the right method depends on your specific application needs, installation requirements, and available equipment. By considering these factors, you can ensure optimal performance and reliability in your fiber optic network.
FAQ
How do you terminate a fiber optic cable?
Terminating a fiber optic cable involves several key steps. First, you strip the protective coating from the fiber. Next, you cleave the fiber to ensure a clean cut. Then, you insert the fiber into the connector or splicing device. Finally, you secure the fiber to complete the termination process.
What tools do you need for fiber optic cable termination?
You need specific tools for fiber optic cable termination. These include a cleaver for precise cutting, a stripper to remove the protective coating, and a crimping tool to secure connectors. For splicing, you may also require a fusion splicer or a mechanical splicer.
What is the difference between connector termination and splicing?
Connector termination allows for easy connection and disconnection of fiber cables. It uses connectors to join cables temporarily. Splicing, however, creates a permanent connection between two fibers. It involves either fusion or mechanical methods to join the fibers seamlessly.
Why is it important to test the connection after termination?
Testing the connection ensures that the termination process was successful. It verifies the integrity and performance of the fiber optic cable. You can use tools like a visual fault locator or an optical power meter to check for any issues or signal loss.
What are the advantages of using SC connectors?
SC connectors offer a push-pull design that provides a secure and reliable connection. They are commonly used in data communication networks due to their ease of use and stability. Their design minimizes signal loss and ensures consistent performance.
How does fusion splicing differ from mechanical splicing?
Fusion splicing uses an electric arc to weld fibers together, creating a strong and durable joint. It offers superior optical performance and is ideal for long-term installations. Mechanical splicing, on the other hand, aligns fibers using a mechanical device. It provides a quick and flexible solution, suitable for temporary or emergency repairs.
What are the benefits of factory termination?
Factory termination ensures high-quality terminations performed in a controlled environment. It reduces installation time since pre-terminated cables arrive ready for use. This method also minimizes labor costs and the risk of errors during installation.
Can you customize cable lengths with field termination?
Yes, field termination allows you to tailor cable lengths to fit specific installations. You can adjust and modify cables on-site to accommodate changes in design or layout. This flexibility ensures a perfect fit for your installation needs.
What makes Dowell's pre-terminated cables reliable?
Dowell's pre-terminated cables undergo rigorous testing to ensure optimal performance and durability. The brand focuses on quality and innovation, ensuring each cable meets the highest standards. These cables simplify the installation process and reduce time and labor costs.
How do you choose between field and factory termination?
Choosing between field and factory termination depends on your specific needs. Field termination offers flexibility and customization, ideal for dynamic environments. Factory termination provides efficiency and quality assurance, suitable for projects requiring consistent and dependable connectivity. Consider your installation requirements and available equipment to make an informed decision.
Post time: Dec-16-2024