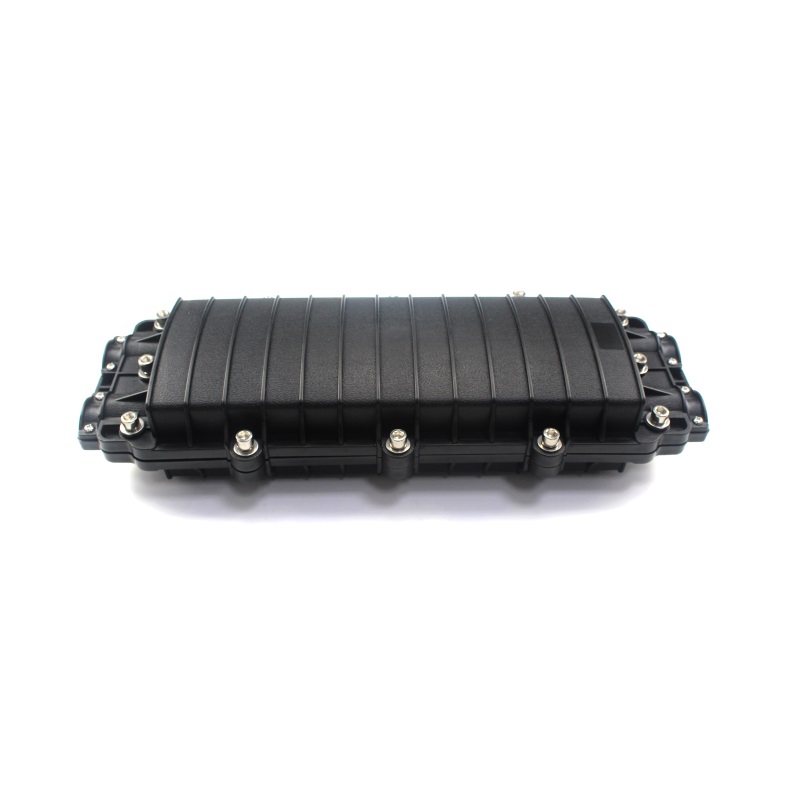
Step 1: Gather Necessary Tools and Materials
Before you begin installing a fiber optic splice closure, ensure you have all the essential tools and materials. This preparation will streamline the process and help you avoid unnecessary delays.
Essential Tools
-
Fiber Optic Stripper: You need this tool to remove the outer jacket of the fiber optic cables. It ensures a clean and precise cut, which is crucial for maintaining the integrity of the fibers.
-
Fusion Splicing Machine: This machine is vital for joining the fiber optic cables. It aligns and fuses the fibers with precision, ensuring a strong and reliable connection.
-
Heat Gun: Use a heat gun to apply heat shrinkable sleeves over the spliced area. This tool helps protect the splices from environmental damage.
Required Materials
-
Fiber Optic Cables: These are the core components of your network. Ensure you have the correct type and length of cables for your installation.
-
Heat Shrinkable Sleeves: These sleeves provide protection for the spliced fibers. They are available in various materials, such as PVC and Polyolefin, each offering unique properties to suit different projects.
-
Splice Closure Kit: This kit contains all the necessary components to assemble and seal the splice closure. Make sure all parts are present and in good condition before starting the installation.
“Access product specification sheets, articles, case studies, white papers, standard recommended procedures, and applications engineering notes on our products and solutions.” This quote emphasizes the importance of understanding the specifications and recommended procedures for the tools and materials you use.
By gathering these tools and materials, you set the stage for a successful installation. Proper preparation ensures that you can focus on executing each step with precision and care.
Step 2: Prepare the Fiber Optic Cables
Proper preparation of fiber optic cables is crucial for a successful installation. You must handle the cables with care to maintain their integrity and ensure optimal performance.
Stripping the Cables
To begin, use a fiber optic stripper to remove the outer jacket of the cables. This tool allows you to expose the fibers without causing damage. Ensure you follow the manufacturer’s guidelines for the correct stripping length. Installation Expert advises, “Following the steps outlined above will help ensure a successful installation, protecting and managing fiber optic cables for optimal performance.” By adhering to these best practices, you safeguard the fibers and set the stage for a reliable connection.
Cleaning the Fibers
Once you’ve stripped the cables, it’s essential to clean the exposed fibers. Use isopropyl alcohol and a lint-free cloth to remove any dust or debris. This step is vital because contaminants can affect the quality of the splice. Technicians emphasize, “By following these guidelines and paying close attention to the installation, termination, and testing processes, technicians can ensure a successful fiber optic installation that performs as required and delivers optimal performance.” Clean fibers contribute to a strong and efficient network, reducing the risk of signal loss.
“By following these best practices, you can ensure that the fiber optic cabling installation is done correctly, and that the cables are properly protected, tested, and maintained,” says Cable Expert. Always consult the cable manufacturer’s specifications to determine the appropriate practices for your specific cables.
By carefully stripping and cleaning the fibers, you lay the groundwork for a successful splicing process. These steps are fundamental to achieving a high-quality installation that meets industry standards.
Step 3: Splice the Fibers
Setting Up the Fusion Splicing Machine
To begin splicing, you must set up the fusion splicing machine correctly. This machine plays a crucial role in ensuring a strong and reliable connection between fiber optic cables. Follow the manufacturer’s instructions to calibrate the machine. Proper calibration ensures that the machine aligns and fuses the fibers with precision. Pay attention to the twist and bend of the fiber during this process. This step is vital for maintaining the integrity of the splice.
“Fusion splicing uses an electric arc or specialized machine to fuse glass fiber ends together,” explains the Fusion Splicing Best Practices document. This method creates a reliable joint with near-zero back reflection and minimal insertion loss.
Performing the Splice
Once the machine is set up, you can proceed to perform the splice. Align the fibers carefully within the machine. The alignment process is critical for achieving a seamless connection. After aligning the fibers, use the machine to fuse them together. This step involves melting the fiber ends to create a permanent bond.
According to the Fusion Splicing vs. Mechanical Splicing document, “Fusion splicing involves melting and fusing the fibers together to create a permanent connection.” This technique ensures a durable and efficient splice.
By following these steps, you ensure that the fibers are spliced accurately and securely. Proper splicing enhances the performance of your fiber optic network, reducing the risk of signal loss and improving overall reliability.
Step 4: Secure and Protect the Splices
Applying Heat Shrinkable Sleeves
To secure your splices, you need to apply Heat Shrink Sleeves over the spliced area. These sleeves provide a seamless, adhesive-lined insulation that protects the fibers from environmental damage. Begin by placing the sleeves carefully over each splice. Ensure that they cover the entire spliced section. Once positioned, use a heat gun to shrink the sleeves. The heat causes the sleeves to contract, forming a tight seal around the fibers. This process not only insulates the splices but also prevents moisture, dust, and chemicals from penetrating the joint.
“Heat shrink sleeves are widely used in the industry to provide seamless, adhesive-lined insulation over joints,” notes the product description. By following these guidelines, you extend the life and performance of your fiber optic connections.
Additional Protective Measures
After applying the heat shrink sleeves, take additional steps to ensure all splices are properly covered and secured. Organize the spliced fibers within the Fiber Optic Splice Tray (FOST). This tray helps manage the fibers and provides an extra layer of protection. Wind the remaining fiber optic cables into a ring with a diameter of at least 80mm. Place this ring into the FOST along with the protective sleeves. This arrangement minimizes stress on the fibers and maintains their integrity.
“Shrink sleeves adhere tightly to objects, providing superior electrical insulation and protection against external agents,” explains the product description. By using these sleeves and organizing the fibers correctly, you enhance the durability and reliability of your network.
By securing and protecting the splices with heat shrink sleeves and additional measures, you ensure a robust and long-lasting fiber optic installation. These steps are crucial for maintaining the performance and reliability of your network.
Step 5: Assemble and Seal the Closure
Arranging the Splices Inside the Closure
You need to organize the splices neatly within the Fiber Optic Splice Closure. Proper arrangement prevents damage and ensures the longevity of your network. Begin by placing each spliced fiber into the designated slots or trays within the closure. This step is crucial for maintaining the integrity of the fibers. Avoid bending or pinching the cables, as this can lead to signal loss or fiber breakage.
“Properly managing fiber cables within the closure prevents bending or pinching, which can damage the fibers,” advises industry experts. By following these best practices, you enhance the reliability of your fiber optic system.
Sealing the Closure
Once you have arranged the splices, it’s time to seal the Fiber Optic Splice Closure. Follow the instructions provided in your splice closure kit carefully. These guidelines ensure that you seal the closure effectively, protecting the splices from environmental factors like moisture and dust. Start by securing the closure body over the cable gland. Use the sealing tape included in the kit to cover any gaps. This step is vital for preventing water ingress and maintaining a stable connection.
“Best Practices for Installing Fiber Optic Splice Closure include properly managing fiber cables within the closure to prevent damage and ensuring successful splicing by preparing fiber optic cables correctly,” states the product description. By adhering to these instructions, you safeguard your network against potential issues.
By arranging the splices neatly and sealing the closure properly, you complete the installation process with precision. These steps are essential for ensuring a robust and reliable fiber optic network. Proper assembly and sealing not only protect the splices but also contribute to the overall performance and efficiency of your system.
You have now learned the five essential steps to install a Fiber Optic Splice Closure. Each step plays a crucial role in ensuring a successful and secure installation. By gathering the necessary tools, preparing the cables, splicing the fibers, securing the splices, and sealing the closure, you enhance the reliability of your network. Remember, following these steps meticulously prevents signal loss and minimizes the risk of costly repairs. Always adhere to safety precautions and industry standards to maintain system integrity. Proper documentation of the installation process further ensures efficiency and reliability.
See Also
Improving Network Links Through Fiber Optic Splice Closures
6 Essential Tips for Choosing the Right Fiber Patch Cord
Boosting Connections: A Guide to Fiber Optic Adapters
Ensuring Long-Term Connectivity with Reliable Fiber Optic Clamps
Maximizing Efficiency in Fiber Optic Cable Testing Procedures
Post time: Nov-13-2024